KAIZEN Yaklaşımı ile OEE İyileştirme
KAIZEN Yaklaşımı ile OEE İyileştirme
OEE (Overall Equipment Effectiveness), üretim süreçlerinde kullanılan makinelerin ve ekipmanların ne kadar etkili çalıştığını ölçmek için kullanılan bir performans göstergesidir. OEE’nin üç ana bileşeni olan kullanılabilirlik, performans ve kalite, üretimin genel etkinliğini anlamak için kritik veriler sunar. Bu bileşenlerin iyileştirilmesi, üretim süreçlerinde daha az duraklama, daha yüksek hız ve daha az hata ile sonuçlanır. İşte bu noktada KAIZEN ve SMED yaklaşımları, süreçlerin optimize edilmesi için etkili araçlar sunar. Bu iki yöntem, yalnızca performansı artırmakla kalmaz, aynı zamanda üretim sürecini daha sürdürülebilir ve kârlı hale getirir.
KAIZEN Yaklaşımı ile OEE İyileştirme
KAIZEN, sürekli iyileştirme anlamına gelir ve işletmelerin her seviyesinde küçük ama sürekli değişikliklerle büyük sonuçlar elde etmeyi amaçlar. Bu yaklaşım, OEE'yi artırmak için hem bireysel hem de ekip bazında iyileştirme çalışmalarını teşvik eder. KAIZEN, sadece makineler ve ekipmanlar üzerinde değil, aynı zamanda iş süreçlerinde, organizasyonel yapı üzerinde ve çalışanların motivasyonunda da olumlu etkiler yaratır.
Atıkların Azaltılması
KAIZEN’in temel ilkelerinden biri, süreçteki atıkları tespit etmek ve ortadan kaldırmaktır. Üretim sırasında gereksiz hareketler, malzeme israfı, enerji kaybı gibi unsurlar verimliliği düşürür. Bu atıkların sistematik bir şekilde ele alınması, süreçlerin daha akıcı ve etkili olmasını sağlar.Çalışan Katılımının Artırılması
KAIZEN, çalışanların aktif katılımını esas alır. Sahadaki çalışanların günlük işlerinde karşılaştıkları sorunlara dair fikir ve çözümleri önemseyerek, süreç iyileştirme çalışmalarına dahil edilmeleri sağlanır. Bu, yalnızca OEE’yi iyileştirmekle kalmaz, aynı zamanda ekiplerin motivasyonunu artırır ve daha uyumlu bir iş ortamı yaratır.Standartlaştırma
KAIZEN ile elde edilen iyileştirmelerin kalıcı olması için standart iş prosedürleri oluşturulur. Standartlaştırma, her çalışanın aynı kalite seviyesinde iş yapmasını sağlar ve performans dalgalanmalarını en aza indirir. Bu, özellikle büyük ölçekli üretim hatlarında kritik bir avantaj sunar.Sorunların Kök Neden Analizi
KAIZEN yaklaşımı, yüzeydeki belirtileri değil, problemlerin kök nedenlerini ele alır. Örneğin, sürekli arıza yapan bir ekipmanın yalnızca onarılması değil, bu arızanın neden kaynaklandığının bulunması ve ortadan kaldırılması hedeflenir. Bu yöntem, tekrarlayan sorunların önlenmesiyle OEE performansını uzun vadede artırır.
KAIZEN uygulamalarında kullanılan 5S, Balık Kılçığı Diyagramı ve PDCA döngüsü gibi araçlar, iyileştirme çalışmalarını daha etkili hale getirir. Bu araçlar, ekiplerin daha düzenli ve hedefe odaklı bir şekilde çalışmasına olanak tanır.
SMED Yaklaşımı ile OEE İyileştirme
SMED (Single-Minute Exchange of Dies), üretim süreçlerindeki ekipman değişim sürelerini bir dakika içinde veya buna yakın bir sürede gerçekleştirmek için kullanılan bir yöntemdir. OEE’nin kullanılabilirlik bileşenini artırmada SMED oldukça etkilidir. Özellikle sık sık üretim değişikliği yapılan sektörlerde, SMED yaklaşımı ile hem zaman kaybı azaltılır hem de üretim esnekliği artırılır.
Ekipman Değişim Sürelerinin Analizi
SMED’in ilk adımı, mevcut ekipman değişim süreçlerinin analiz edilmesidir. Bu analizde, değişim sırasında yapılan işlemler iç süreçler (makine durduğunda yapılan işlemler) ve dış süreçler (makine çalışırken yapılan işlemler) olarak ikiye ayrılır. Analiz sayesinde verimsizliklerin nereden kaynaklandığı daha net bir şekilde anlaşılır.İç ve Dış Süreçlerin Ayrıştırılması
Verimliliği artırmak için iç süreçler minimuma indirilirken, dış süreçler mümkün olduğunca optimize edilir. Örneğin, bir ekipmanın değişimi sırasında yapılan hazırlıkların çoğu, ekipman çalışırken tamamlanabilir. Bu, duraklama sürelerini büyük ölçüde azaltır.Standardizasyon ve Basitleştirme
SMED ile süreçler basitleştirilir ve standartlaştırılır. Her değişim için aynı prosedürün izlenmesi, hataları azaltır ve değişim sürelerini kısaltır. Ayrıca, çalışanların bu prosedürlere daha hızlı adapte olmasını sağlar.Hızlı Bağlantı Sistemleri Kullanımı
SMED, hızlı bağlantı elemanlarının ve modüler ekipmanların kullanımını teşvik eder. Bu teknolojiler, değişim sürelerini birkaç dakikaya kadar düşürerek büyük zaman tasarrufu sağlar. Özellikle otomotiv ve ambalaj sektöründe bu tür uygulamalar yaygındır.Simülasyon ve Eğitim
Çalışanların SMED uygulamalarını etkin bir şekilde kullanması için eğitim programları düzenlenir. Simülasyonlarla yapılan pratikler, sürecin daha hızlı ve doğru bir şekilde gerçekleştirilmesine yardımcı olur. Eğitimler aynı zamanda çalışanların süreçlere olan güvenini artırır.
KAIZEN ve SMED’in Birlikte Kullanımı
KAIZEN ve SMED yaklaşımlarının birlikte kullanılması, OEE performansını daha kapsamlı bir şekilde iyileştirmeyi mümkün kılar. KAIZEN, süreçlerin genel organizasyonunu ve sürekli iyileştirilmesini sağlarken, SMED belirli süreçlerin optimize edilmesine odaklanır. Örneğin, KAIZEN ile standart iş prosedürleri oluşturulabilirken, SMED bu prosedürlerin daha hızlı uygulanmasını sağlayabilir.
Bakmadan Geçme
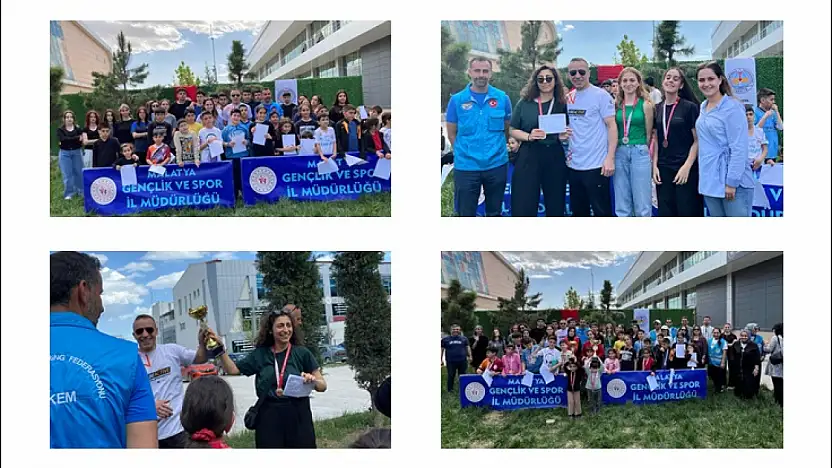
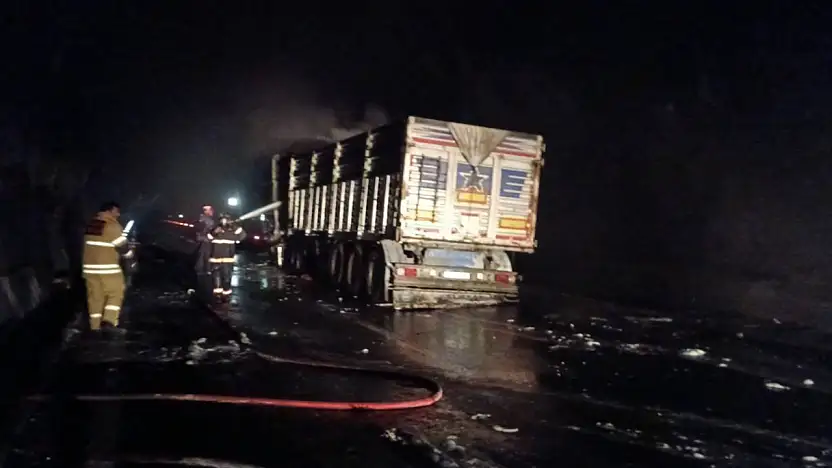
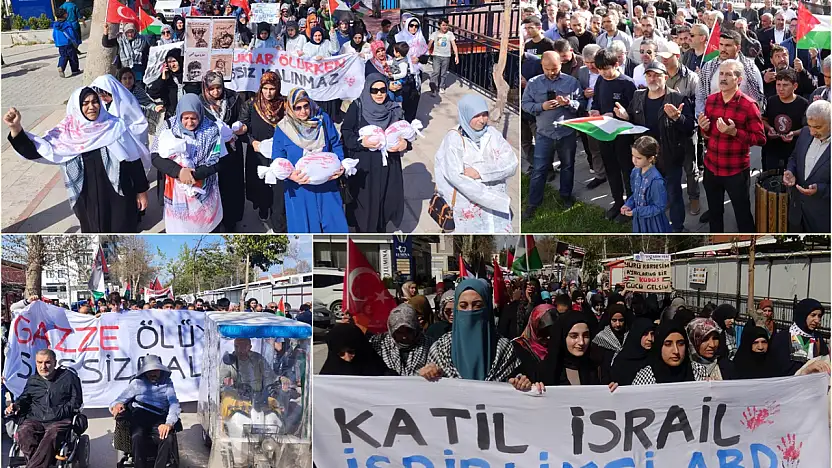
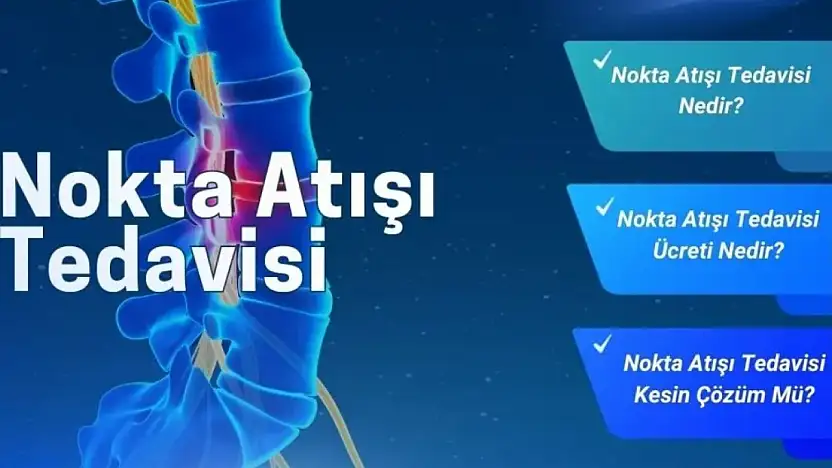
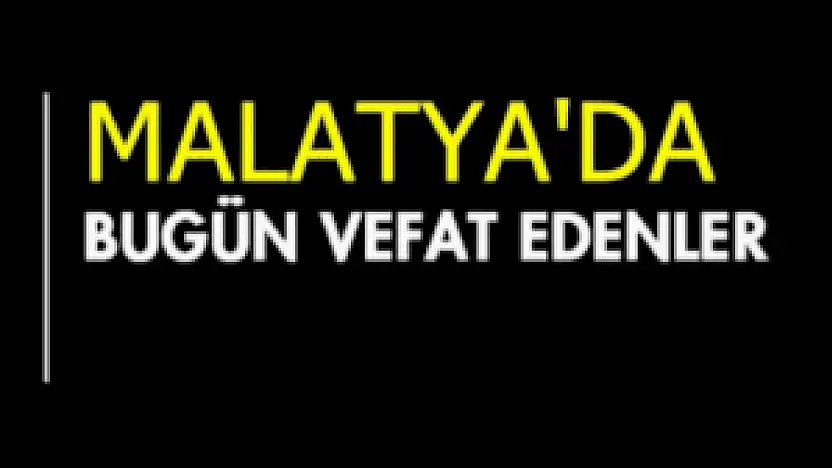
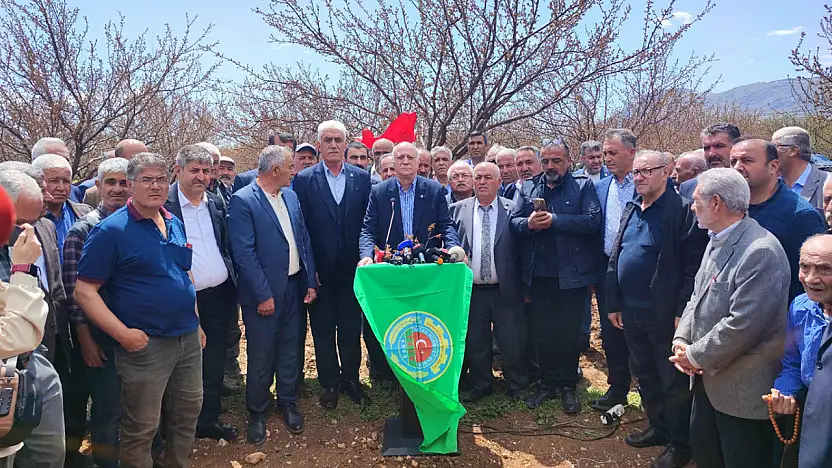